Field Studies
Some of the industrial engines that we have been long term testing include:

Nordberg diesel generator:
- 4800hp engine designed for ships
- 5 years operating with device
- Generator 3.2 megawatts
- Operating continuously for several months at a time (during the summer, dry, seasons when water turbines are not useable
Results:
- Improved power and response to power changes
- Reduced vibration significantly
- Reduced sound
- Reduced cylinder head temperatures
- Reduced smoke and toxic emissions
- Easier starting characteristics
- Improved combustion allowed the use of heavier, cheaper, diesel fuel
- Reduction in C02 emission
- Cleaner intercooler and carbon deposits on engine
In comparison, none of the other engines, without the device, could use the heavier fuels without smoking excessively.
Garbage Trucks (3)

- -Engines have considerably more power and acceleration
- -Reduction in smoke 80o/o-95%
- -Cleaner engine oil
- -Quieter and smoother
- -Easier starting
- -Reduced C02
- operating 5 days per week for over two years
- no required maintenance on devices
- no required engine service, other than oil changes on older engines
- new engine had significantly reduced maintenance issues on existing emission control equipment e.g. EGR valve was replaced twice in one year before the device was installed, but after it required no further replacement in one and a half years.
School Buses
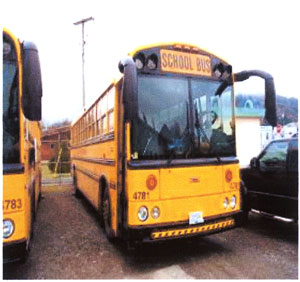
- -Reduced vibration and sound
- drivability
- -Elimination of open crankcase vent-tube
- -Reduced exhaust odor
- -Reduced exhaust emissions 60%- 85%
- -Oil cleanliness improved
- -100% driver satisfaction

- Five buses were tested
- -The elimination of the open vent tube reduced crankcase emissions to zero exposure
- -Vacuum created in crankcase reduced oil leaks

Fire Trucks
- -Starting improved dramatically
- -Smoke and exhaust smell is now virtually unnoticeable
- -Speed increase 1Om ph on the highway
- -Acceleration and drivability improved
- -Vibration and sound reduction reduced significantly (many firemen noticed these changes)



Cement Trucks and Gravel Trucks
10 tested since May 2006 These engines all had open vent systems and had excessive exhaust smoke. Some had leaking crank seals causing oil to drip into the ground; most job sites consider this unacceptable.

- The emissions level on these trucks dropped significantly approximately 80%. They have been using the device for over one year.

- all engines exhibited noteworthy performance improvements in drivability, acceleration, starting, vibration reduction and sound reduction
- Some engines stopped leaking oil because of the crankcase vacuum, oil remained much cleaner between fresh oil changes
- Emissions reduced dramatically, where as before in some engines thick plumes of black smoke nearly continuously was emitted during normal driving condition was now reduced to invisible emission, a reduction from our estimated 95% opacity to 50%

Tractors and Railroad Equipment
Approximately 25 tractors were tested since 2001, without exception all engines responded with an increase in power. Some engines were PTO dyno tested and indicated power changes e.g. of 127hp before to 158hp after, a substantial increase.
- all engines indicated a reduction in smoke
- all engines had an open vent tube, now enclosed indicated improved exhaust odor and improved oil control, as a result of the vacuum in the crankcase
- vibration, sound levels and starting characteristics all were noteworthy improvements.

Many of these tractors are in commercial environments, where they work every day, all day. There has been only positive feedback. It should be noted however, that during testing and development stages, install characteristics were carefully reviewed and tested. Some preliminary tests proved that installation procedures were very important and if done incorrectly then positive crankcase pressure and poor oil control was noted.
These long term field test provide a solid understanding of how engines respond under extreme conditions and how installation characteristics affect long term use.
All engines tested regardless of operation condition or applications indicated similar results. Some of the other categories, involving long term field testing include:
- -railroad equipment
- -generators
- -compressors
- -boats
- -semis
- -logging equipment
- -delivery trucks
- -loaders
- -tow trucks
- -excavators
- -water tankers
- -bob cats
- -motor homes
- -pickups
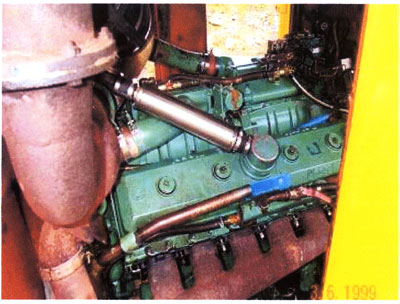

With having 8 years of field research on hundreds of engines, it has been consistently demonstrated that with our technology the performance enhancements are what motivates the consumer to want these emission reducing devices on their engines. Also, most have learned that their engines are lasting longer and running smoother and cleaner. Emissions reducing equipment and strategies have never appealed to most owners of equipment because of the normally detrimental effects on performance, engine maintenance, excessive vibration or increased C02 production. Long term testing verifies that this technology is on the leading edge of combining emissions reduction with performance improvements. Also, what may be the most encouraging aspect is that it works alone and in conjunction with all known existing emissions reduction systems.
Historically, manufacturers of large diesel engines have been able to elude much of the damaging effects crankcase emissions cause to engines, simply releasing the toxins into the atmosphere.

- The poisonous crankcase vapours can often be seen as a fog, as seen in this photo of an industrial diesel engine.

With the growing concerns of our environment's health and the overall detriment to our health that crankcase emissions cause, it becomes crucial to identify and implement a better solution - technology that can effectively process toxic crankcase emissions without any of the detrimental effects associated with filtering, recycling, or releasing these untreated oily vapors.
Currently there is nothing on the market that encloses the crankcase enclosure on existing open vent systems without significantly hindering engine performance. After nearly eight years of field-testing in research and development, we have maximized the efficiency in the design of the device enabling mass production with minimal effort. The current design allows unlimited parameters in flexibility of design such as shape, size or application.
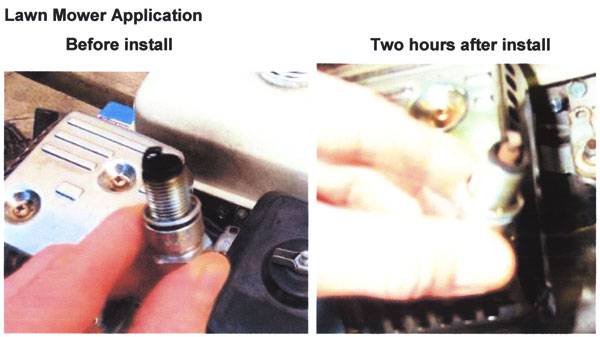
Any size of device desired can be easily manufactured from motorcycles to very large diesel engines in ships. It only requires that sufficient internal volume be allowed for the given application; the technology itself is the same, it only requires scaling to enable adaptation to the various applications.

The sparkplug cleanliness is an indication of clean combustion. Without exception every sparkplug was black and sooty before the installation.
The technology is safe. It does not produce heat or is under any pressure. The gases exiting the device are not as unhealthy as the crankcase gases entering the unit. The modified gases are reactive to fuels and other hydrocarbons such as oil residues. As well, crankcase gases are not under pressure or high heat condition. This allows flexibility and safety in installation unlike fuel processing, or exhaust catalytic converters.
Many engines respond immediately to the installation of this technology. Usually an engine produces noticeably less toxic emissions, runs smoother and quieter within a few minutes. However, the full effects are not realized until the engine has been run and worked sufficiently to allow contaminants to be cleaned from the rings and valves.
As the engine becomes clean and the compression pressures restored, it performs better and better. In many cases this happens in only a few hours and in some extreme cases of extensively contaminated engines it may require over one hundred hours to thoroughly clean. Most importantly, once installed, the unit will allow the engine to remain in service significantly longer. Cleaner engines perform better, last longer and produce less toxic emissions.Many old engines that we have demonstrated this technology on are performing better than they ever have, even better than when they were new.
Cars and Trucks

- Hundreds of cars have been tested over the past seven years. Owners' feedback is as follows:
- -smoother
- -faster
- -cleaner
- -quieter
- -reduced maintenance
- -improved starting
- -cleaner oil

- Several hundred pickups, diesel and gasoline, have been extensively tested, comments:
- -Improved towing
- -Faster acceleration
- -Easier starting
- -Cleaner exhaust
- -Less vibration
- -Cleaner engine oil
- -Less maintenance